Pharmaceutical rubber stoppers serve as closures for vials, bottles, and containers holding a variety of medications, including injectables, vaccines, and sterile formulations. These stoppers are meticulously designed and engineered to create a secure and airtight seal, shielding the contents from external influences that could compromise their quality.
The material composition of these stoppers has evolved significantly to meet the stringent requirements of the pharmaceutical industry. While natural rubber stoppers were previously common, concerns about extractables, leachables, and potential interactions with drug formulations spurred the adoption of synthetic elastomers. Materials such as bromobutyl or chlorobutyl rubber are preferred for their inertness, resilience, and ability to maintain a barrier against contaminants.
Precision in manufacturing processes is crucial to ensure the reliability of pharmaceutical rubber stoppers. Advanced technologies and cleanroom environments are employed to minimize particulate contamination and ensure consistent quality. Automated inspection systems further guarantee dimensional accuracy and integrity, crucial in sterile pharmaceutical environments.
pharmaceutical rubber stoppers undergo extensive testing to validate their compatibility with various drug formulations. These stoppers must not interact with medications, ensuring that the integrity and stability of the drugs remain uncompromised throughout their shelf life.
The importance of these stoppers goes beyond their functional role as mere closures. They are integral to ensuring patient safety by preventing contamination and maintaining the efficacy of medications. A secure seal minimizes the risk of microbial growth or exposure to air and moisture, which could lead to degradation or compromise the potency of the drug.
In the context of injectable medications, the integrity of rubber stoppers is critical in ensuring accurate dosing and administration. Any compromise in the seal could lead to improper dosage or contamination, posing risks to patient health.
Continual research and development efforts aim to enhance the performance of pharmaceutical rubber stoppers. Innovations focus on improving materials, designs, and manufacturing processes to address evolving pharmaceutical needs, such as compatibility with new drug formulations and enhanced safety measures.
The role of pharmaceutical rubber stoppers in medication safety and integrity remains indispensable. Their reliability in creating a protective barrier against external contaminants and their ability to maintain the quality of pharmaceutical products underscore their significance in the pharmaceutical landscape. As technology advances, these stoppers will continue to evolve, contributing to the maintenance of high standards in pharmaceutical packaging and ensuring the safe delivery of medications to patients worldwide.
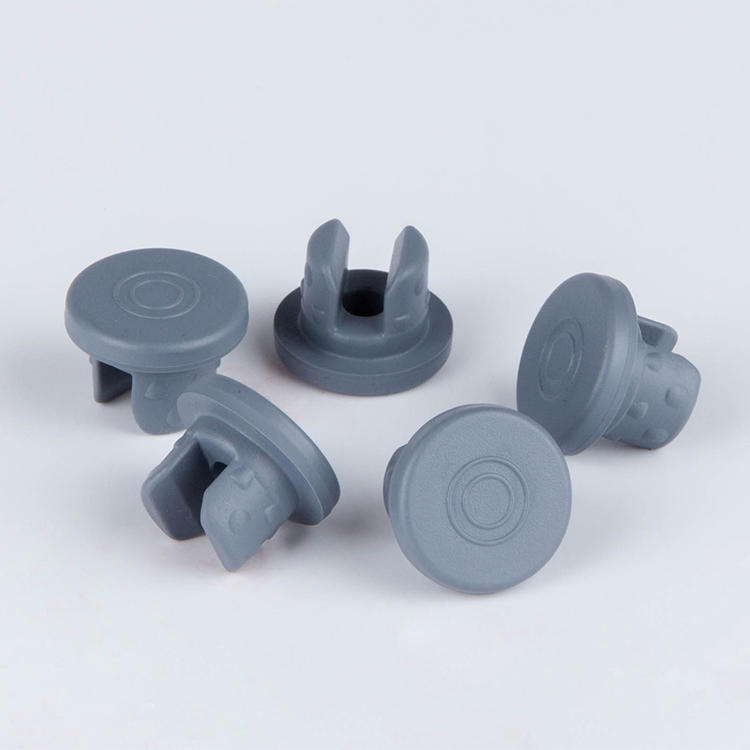