The manufacturing process behind pharmaceutical rubber stoppers demands precision and adherence to stringent quality standards. Cutting-edge technologies are employed to ensure consistency in material composition, dimensional accuracy, and mechanical properties. Such meticulous attention to detail is necessary to meet the rigorous demands of the pharmaceutical industry.
The composition of these stoppers is carefully formulated to be chemically inert, ensuring compatibility with a wide array of pharmaceutical formulations. This inertness is crucial in preventing interactions between the drug and the container, preserving the medication's efficacy and stability throughout its shelf life.
Furthermore, the elasticity and flexibility of rubber stoppers are essential characteristics that allow for easy insertion and removal from containers while maintaining an airtight seal. This feature ensures the integrity of the packaged medication and prevents any compromise to its efficacy or safety.
Sterility is of paramount importance in pharmaceutical packaging, especially for injectable medications. Rubber stoppers create a barrier against microbial contamination, effectively safeguarding the pharmaceutical product from harmful microorganisms. The maintenance of a sterile environment within the container is critical in preserving the medication's potency and preventing potential adverse effects on patients.
The selection of the appropriate rubber stopper for a specific pharmaceutical product is a meticulous process. Factors such as the drug formulation, compatibility, and storage conditions play a pivotal role in determining the ideal stopper to ensure optimal protection and preservation of the medication.
As the pharmaceutical industry evolves, advancements in rubber stopper technology continue to address emerging needs and challenges. Manufacturers are developing specialized stoppers with enhanced features, such as coatings to improve compatibility with sensitive drugs, reduced extractables to minimize substance leaching, and improved resealing properties for multi-use containers.
Quality control is a cornerstone in the production of pharmaceutical rubber stoppers. Rigorous quality assurance measures encompass comprehensive testing protocols, including assessments for dimensional accuracy, resilience, chemical inertness, and sterility. Compliance with these standards ensures the reliability and safety of the final product.
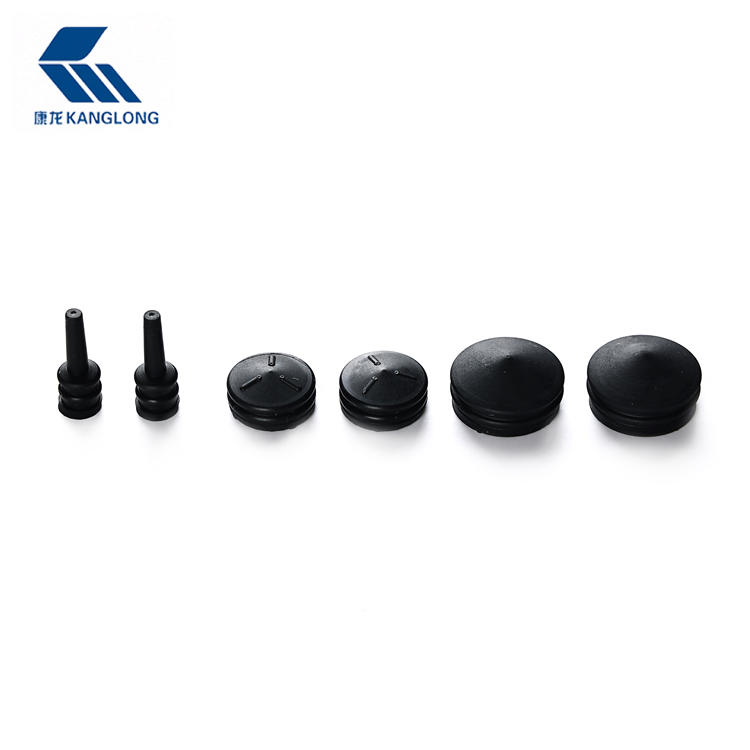