Pharmaceutical rubber stoppers are typically made from high-quality elastomers, such as synthetic rubber or silicone. These materials are chosen for their ability to maintain flexibility, chemical resistance, and compatibility with various pharmaceutical formulations. The stoppers are engineered to withstand the challenging conditions encountered during transportation, storage, and administration of medications.
Maintaining sterility is paramount in the pharmaceutical industry. Pharmaceutical rubber stoppers undergo rigorous sterilization processes, including gamma irradiation or autoclaving, to ensure they are free from microorganisms and contaminants. Additionally, stringent quality control measures are implemented to verify the integrity of the stoppers, including visual inspections and tests to assess factors such as extractables, leachables, and dimensional accuracy.
Pharmaceutical rubber stoppers are designed to be compatible with a wide range of drug formulations, including liquid, solid, and lyophilized (freeze-dried) medications. They are engineered to provide an airtight seal that prevents leakage and evaporation, preserving the drug's potency and efficacy. The stoppers also help to minimize the risk of interaction between the medication and the container, ensuring the stability and safety of the drug formulation.
The safety of pharmaceutical products is of utmost importance. Pharmaceutical rubber stoppers are manufactured in compliance with stringent regulations and standards, such as the Good Manufacturing Practices (GMP) guidelines. These guidelines ensure that the stoppers meet specific requirements for quality, sterility, and performance. Additionally, the stoppers undergo extensive testing to evaluate their compatibility with different drug formulations and packaging materials.
The pharmaceutical industry continuously seeks advancements and innovations in rubber stopper technology. Manufacturers invest in research and development to enhance the performance and functionality of stoppers, including improvements in sealing properties, chemical compatibility, and ease of use. Additionally, innovations such as tamper-evident features and color-coded stoppers for easy identification contribute to medication safety and reduce the risk of medication errors.
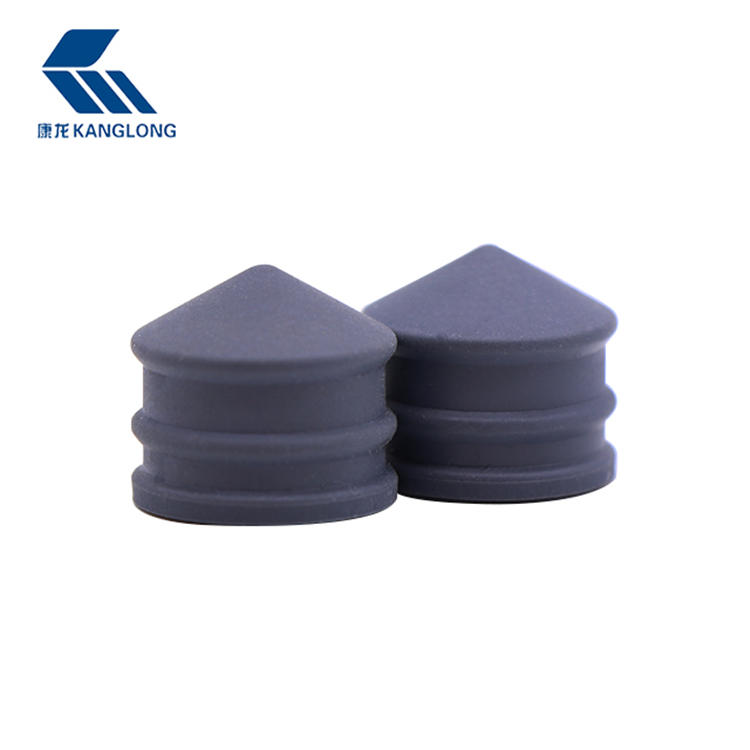