Pharma Rubber Stoppers: A Brief Overview
Pharma rubber stoppers are specialized closures made from elastomeric materials, typically synthetic rubber compounds like bromobutyl or chlorobutyl rubber. They are designed to fit snugly into the neck of pharmaceutical vials or bottles, forming a secure seal that prevents the entry of air, moisture, or foreign particles. This seal is essential to maintain the quality, efficacy, and safety of pharmaceutical products.
Preserving Sterility
Sterility is a paramount concern in pharmaceutical manufacturing. Any contamination can compromise the efficacy of medications and pose serious health risks to patients. Rubber stoppers are a critical barrier between the sterile contents of a vial and the outside environment. They are manufactured under strict conditions to meet stringent quality and cleanliness standards, ensuring that they do not introduce contaminants during the sealing process.
Maintaining Potency
Many pharmaceutical products are sensitive to environmental factors such as light and oxygen. Exposure to these elements can degrade the active ingredients in medications, reducing their potency and shelf life. Rubber stoppers help to create an airtight and light-resistant seal, protecting the contents of the vial from deterioration and ensuring that the medication retains its effectiveness throughout its shelf life.
Preventing Leaks
Effective sealing is not only about keeping contaminants out but also about preventing the contents from leaking out. Rubber stoppers are designed to provide a leak-proof seal, preventing any liquid or gas from escaping. This is especially crucial for injectable medications, where precise dosing and sterility are non-negotiable.
Compatibility and Material Selection
The choice of rubber material for stoppers is a critical decision for pharmaceutical manufacturers. Different medications may require different types of rubber to ensure compatibility. For instance, some drugs may interact with certain rubber compounds, leading to degradation or chemical reactions. Manufacturers must carefully select the appropriate rubber material to guarantee the safety and efficacy of their products.
Quality Control and Regulation
Pharma rubber stoppers are subject to stringent quality control measures and regulations to meet the highest industry standards. Regulatory authorities, such as the U.S. Food and Drug Administration (FDA) and the European Medicines Agency (EMA), closely monitor the manufacturing and use of rubber stoppers to ensure patient safety.
Pharma rubber stoppers may be small in size, but their role in pharmaceutical packaging is immense. They are the unsung heroes that ensure the safety, sterility, and integrity of medications. As pharmaceutical innovations continue to advance, so too will the materials and technologies used in rubber stopper manufacturing. The future of pharmaceutical packaging will likely see even more precise and specialized rubber stoppers, contributing to the industry's commitment to delivering safe and effective medications to patients worldwide. In the world of pharmaceuticals, every detail counts, and pharma rubber stoppers are a testament to that commitment.
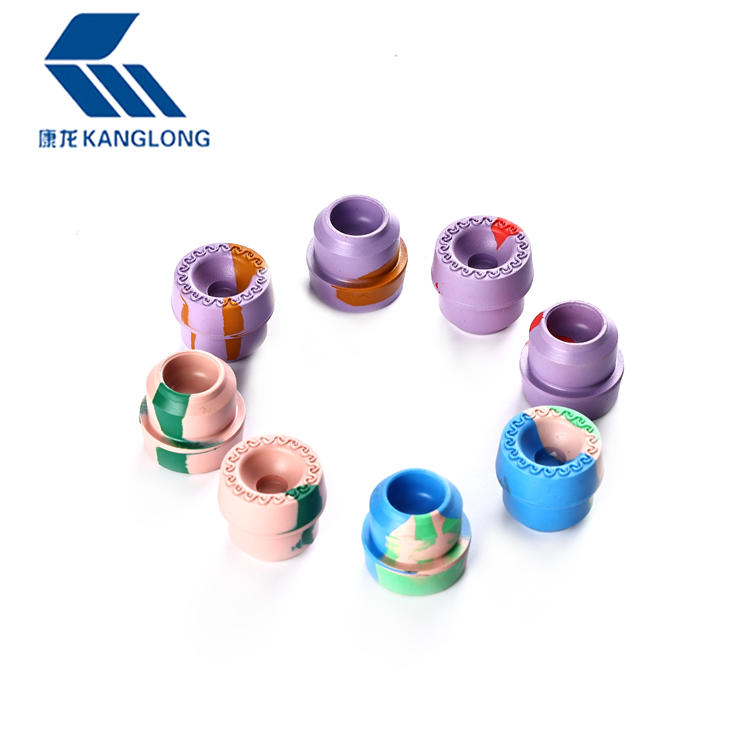