The Role of Pharma Rubber Stoppers
Pharma rubber stoppers are essential in the pharmaceutical industry because they act as a barrier, preventing external contaminants from entering medication containers. Contamination can compromise the safety and efficacy of drugs, which is especially concerning in the context of patient health. Rubber stoppers help maintain a sterile environment inside the vial or container, ensuring the medication's quality remains intact until it reaches the patient.
Characteristics of Pharma Rubber Stoppers
Pharma rubber stoppers possess several key characteristics that make them suitable for use in pharmaceutical packaging:
Chemical Resistance: Rubber stoppers are designed to resist chemical reactions, which is crucial when they come into contact with various drugs and their formulations. This resistance helps prevent the rubber from degrading and affecting the medication.
Elastomeric Properties: Rubber stoppers have excellent elastomeric properties, allowing them to provide an effective seal. They can expand and contract to adapt to the container's neck, ensuring a tight closure.
Sterility: Sterility is paramount in pharmaceuticals. Rubber stoppers undergo rigorous sterilization processes to ensure that they do not introduce harmful microorganisms into the medication.
Low Extractables: Pharma rubber stoppers are designed to release minimal extractable substances into the drug product. This minimizes the risk of chemical interactions that could compromise the medication.
Customizability: Manufacturers can customize rubber stoppers to fit various container types and accommodate specific drug formulations. This versatility ensures a secure and tailored sealing solution for different medications.
Manufacturing Process
The production of pharma rubber stoppers is a meticulous process to guarantee their quality and safety. The manufacturing process typically involves the following steps:
Raw Material Selection: High-quality elastomers, such as butyl rubber, bromobutyl rubber, and chlorobutyl rubber, are chosen as the base materials for the stoppers.
Mixing and Compounding: The selected rubber material is mixed with curing agents and other additives to achieve the desired properties. The compound is then processed into sheets or pellets.
Molding and Shaping: The rubber compound is shaped into the final stopper form through injection or compression molding. This step includes the creation of the stopper's top, bottom, and skirt.
Vulcanization: The stoppers are vulcanized to improve their durability and elasticity, ensuring they can withstand the stress of sealing containers.
Quality Control: Rigorous quality control tests are conducted to verify the physical, chemical, and biological properties of the rubber stoppers. This includes testing for sterility, extractables, and dimensional accuracy.
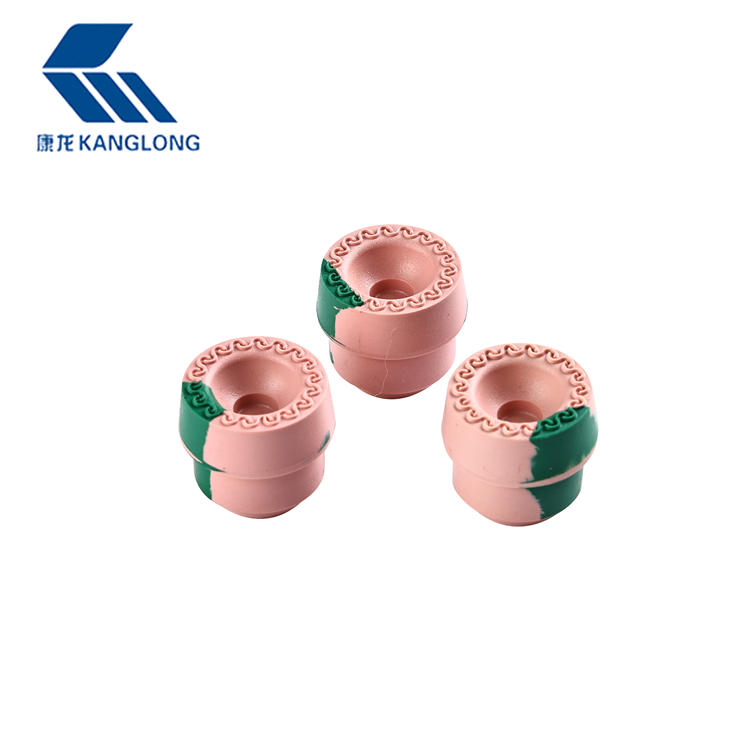