Pharma rubber stoppers have evolved significantly over time, undergoing meticulous development to meet stringent quality standards. Initially, natural rubber stoppers were prevalent in the pharmaceutical industry. However, concerns regarding extractables, leachables, and their potential interaction with drugs prompted advancements in materials and manufacturing processes.
Modern rubber stoppers used in pharmaceutical packaging are predominantly made from synthetic elastomers like bromobutyl or chlorobutyl rubber. These materials offer superior properties such as excellent resilience, gas permeability resistance, and minimal interaction with drug formulations, ensuring the stability and safety of medications.
The design and composition of pharma rubber stoppers are engineered with precision to serve specific functions. They provide an airtight seal, preventing the ingress of contaminants, moisture, and oxygen that could compromise the efficacy and shelf life of pharmaceutical products. Furthermore, they offer compatibility with various drug formulations, including sterile injectables, vaccines, and parenteral medications.
The manufacturing process of these stoppers involves stringent quality control measures. Advanced technologies, including cleanroom production environments and automated inspection systems, are employed to ensure the highest standards of cleanliness and dimensional accuracy. This meticulous approach minimizes particulate contamination, crucial in sterile pharmaceutical environments.
the development of specialized coatings and treatments for rubber stoppers has further enhanced their performance. Siliconization, a process where a thin layer of silicone is applied to the stopper surface, facilitates smoother insertion into vials and syringes, reducing friction and the risk of coring—a process where small rubber particles break off and contaminate the medication.
The significance of pharma rubber stoppers extends beyond mere functionality; they also play a pivotal role in patient safety. A reliable seal prevents microbial contamination, safeguarding the potency and purity of medications administered to patients. In the context of injectable medications, their integrity directly impacts dosage accuracy and efficacy, making them a critical component of healthcare delivery.
As pharmaceutical technologies continue to advance, the role of rubber stoppers evolves in tandem. Ongoing research focuses on developing innovative materials and designs that offer enhanced performance, sustainability, and compatibility with evolving drug formulations and packaging needs.
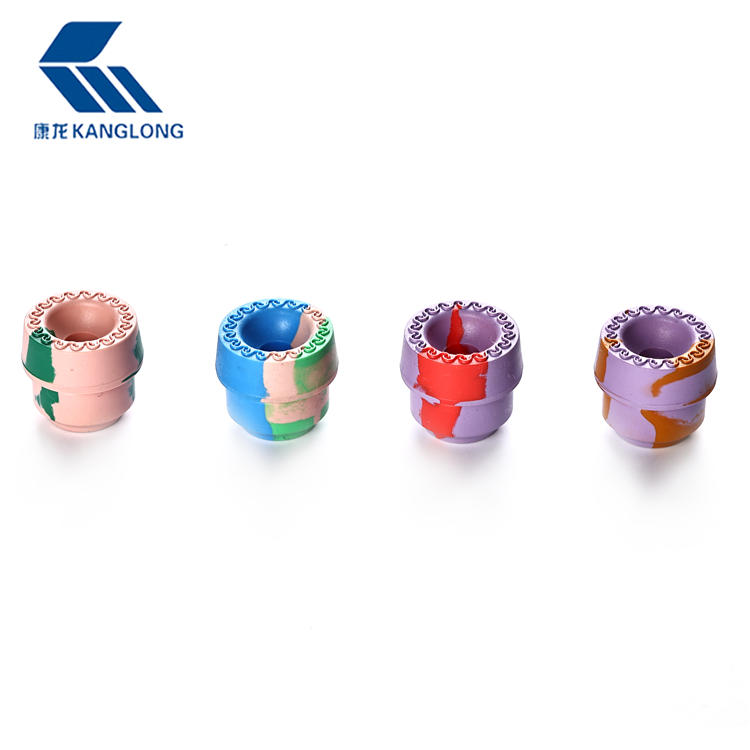