The coating on rubber stoppers serves as a barrier, protecting the contents of pharmaceutical containers from external factors such as moisture, gases, and contaminants. This barrier helps maintain the stability and quality of the drug formulation, extending its shelf life and preserving its potency. Coated rubber stoppers are engineered to be chemically compatible with a wide range of drug formulations, ensuring that the stopper does not react with or adversely affect the medication.
Maintaining sterility is paramount in pharmaceutical packaging. Coated rubber stoppers undergo stringent sterilization processes to ensure they are free from microorganisms and contaminants. The coating's smooth surface reduces the adherence of particles and minimizes the risk of shedding, preventing particulate contamination that could compromise the quality and safety of medications. The combination of sterility and contamination prevention measures provides added assurance for pharmaceutical manufacturers and healthcare professionals.
Certain medications are sensitive to interaction with container materials, potentially leading to drug degradation or altered efficacy. Coated rubber stoppers help mitigate this risk by providing a barrier between the drug formulation and the rubber surface. The coating acts as a protective layer, reducing the potential for leaching or absorption of substances from the stopper into the medication. This safeguard ensures that the drug maintains its intended properties and effectiveness.
Coated rubber stoppers adhere to stringent quality control measures and regulatory standards within the pharmaceutical industry. Manufacturers conduct extensive testing to verify the coating's integrity, durability, and compatibility with different drug formulations. Compliance with regulations such as Good Manufacturing Practices (GMP) ensures that coated rubber stoppers meet specific requirements for quality, performance, and safety.
The field of coated rubber stoppers continues to evolve with innovative solutions and customization options. Manufacturers invest in research and development to improve the performance, chemical resistance, and functionality of coatings. Customized coatings can be tailored to meet the specific requirements of different drug formulations, ensuring optimal compatibility and performance. Additionally, coatings can incorporate features such as color-coding or unique identifiers, aiding in visual identification and preventing medication errors.
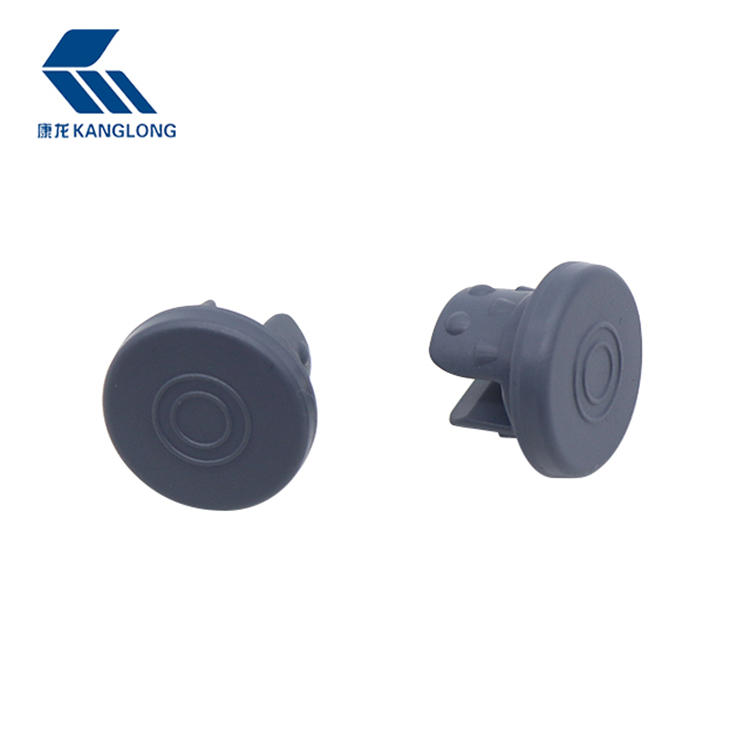